A compressor is a mechanical device designed to increase gas pressure by reducing its volume. These devices are critical in many industrial and domestic applications as they convert low pressure gas into high pressure gas suitable for various purposes. Compressors operate on principles based on thermodynamics, fluid mechanics and mechanical engineering. Every mechanical and electrical company relies on compressors to improve the efficiency and productivity of various operations.
The core principle of a compressor’s operation involves the intake of gas at a low pressure, which is then compressed through one or more stages to increase its pressure. This compression is typically achieved using reciprocating pistons, rotating impellers, or helical screws. The energy required for this process is supplied mechanically or through a power source like electricity.
Types of Compressors
Piston Compressors
Also known as reciprocating compressors, they use pistons driven by a crankshaft to deliver gases at high pressure.
Screw Compressors
These use two helical screws to compress gas. They are known for their efficiency and are commonly used in industrial applications.
Centrifugal Compressors
These use a rotating impeller to increase gas pressure and are often used in high-flow applications such as gas turbines.
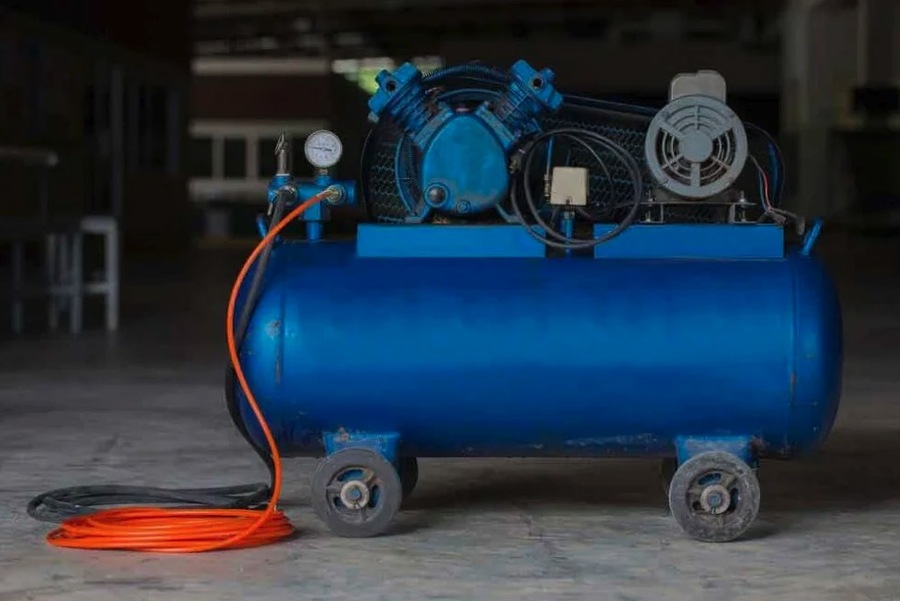
Historical Development of Compressors
Early Innovations
The journey of compressor technology began in the 17th century. In 1650, German physicist Otto von Guericke, inspired by Evangelista Torricelli’s discovery of the vacuum phenomenon, constructed the first single-stage piston compressor. Guericke’s innovation marked the beginning of artificial vacuum creation and air compression technologies.
In 1765, Russian scientist Ivan Polzunov made significant advancements by creating a two-piston steam engine with a power output of 1.8 horsepower for industrial use. This invention utilized the energy of compressed hot steam to alternately move pistons, greatly enhancing industrial capabilities and marking a major milestone in the history of compressors.
Advancements in Thermodynamics and Efficiency
From the 17th to the 19th centuries, significant advancements in thermodynamics profoundly influenced compressor technology. Key contributions came from scientists like Robert Boyle (1662), Edme Mariotte (1676), Joseph Fourier (1822), Sadi Carnot (1824), Julius von Mayer and James Joule (1840s), Émile Clapeyron (1834), and Dmitri Mendeleev (1874). These scientists’ work on gas laws, heat transfer, and thermodynamic cycles helped solve efficiency loss issues due to increased gas temperature under high pressure.
This period also saw the introduction of multi-stage compressors equipped with intermediate and after-coolers for compressed air. These improvements in sealing and forced cooling of the pumping unit significantly enhanced compressor efficiency and durability.
Diversification and Technological Breakthroughs
By the end of the 19th century, compressors were used not only to compress air but also other gases. In 1850, American physician John Gorrie demonstrated the production of artificial ice using compression cycle technology, which is the basis for modern refrigeration. He utilized ammonia as a working gas, showcasing the potential of compressors beyond traditional applications.
In March 1878, German engineer Heinrich Krigar patented the concept of screw compressors. However, the manufacturing technology of the time could not produce the complex screw pair required. It wasn’t until later advancements in manufacturing processes that screw compressors became viable, leading to widespread use in various industries.
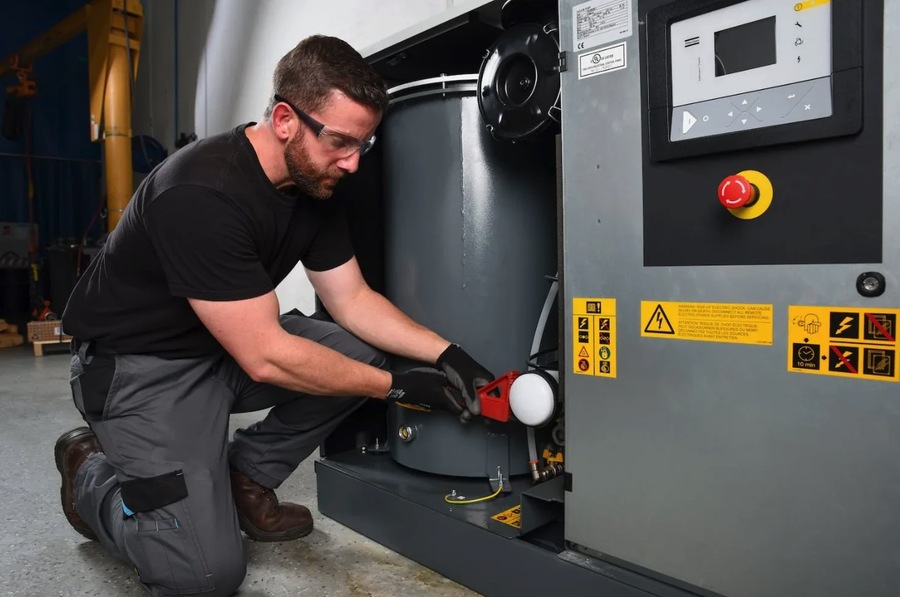
Modern Applications of Compressors
Gas and Oil Industry
In the gas and oil industry, compressors play a crucial role in extracting and transporting hydrocarbons. They are used to drill wells, lift minerals, and compress, collect, and transport fossil fuels through pipelines. Compressors ensure that natural gas, oil, and other resources are efficiently moved from extraction sites to processing plants and distribution centers.
Transportation
Compressors are integral to the transportation sector. They provide compressed air for turbojet engines, airplane cabins, and submarines, ensuring these vehicles operate effectively and safely. The braking systems of trains and the operation of internal combustion engines also rely heavily on compressors to function properly.
Energy Sector
The energy sector relies on compressors for the smooth operation of power plants. Compressors are essential in gas turbines and other machinery, ensuring stable and efficient energy production. Their ability to handle large volumes of gas at high pressures makes them indispensable in power generation.
Food Industry
In the food industry, compressors are used in refrigeration units, working tools, packaging, and mixing machines. They play a critical role in ensuring food products are stored, processed, and packaged under optimal conditions. Compressed air is essential in maintaining the quality and safety of food products from production to consumer delivery.
Construction
Compressors supply compressed air to construction pneumatic tools such as jackhammers, sandblasters, and concrete breakers. They are essential for various tasks, including removing asphalt layers and laying cement in road installation works. Construction sites rely on compressors to power tools that make heavy-duty tasks manageable and efficient.
Road Installation Works
In road installation, construction compressors remove layers of asphalt, and tools powered by compressors are used to lay cement. These compressors enable efficient and precise work, ensuring roads are built and maintained to high standards. The power and reliability of compressors make them a vital component in infrastructure development.
Medicine and Pharmaceuticals
In medicine and pharmaceuticals, compressors are used in dentistry, breathing apparatus, and the manufacture and packaging of medicines. They ensure that medical tools operate effectively and that medications are produced under precise conditions. Compressors are crucial in maintaining the sterile and controlled environments required in these fields.
Household Use
Portable compressors have found a place in everyday life due to their efficiency, cost-effectiveness, and safety. They are used for tasks such as tire inflation, painting, and operating small pneumatic tools. Compressors are a convenient and practical tool for various household applications, making everyday tasks easier and more efficient.
Conclusion
Compressors have evolved significantly since their inception in the 17th century. Today, they are indispensable in various industries, from the gas and oil sector to household applications. Their ability to efficiently compress gases underpins many modern technologies, making them a cornerstone of industrial and domestic processes.
In regions like the UAE, compressors are widely used, reflecting their critical role in both industrial and everyday applications. Given their technical complexity, the maintenance and repair of compressors should always be entrusted to professionals to ensure their optimal performance and longevity. Whether in large-scale industrial operations or everyday household tasks, compressors continue to be an essential technology, driving efficiency and innovation across the globe.
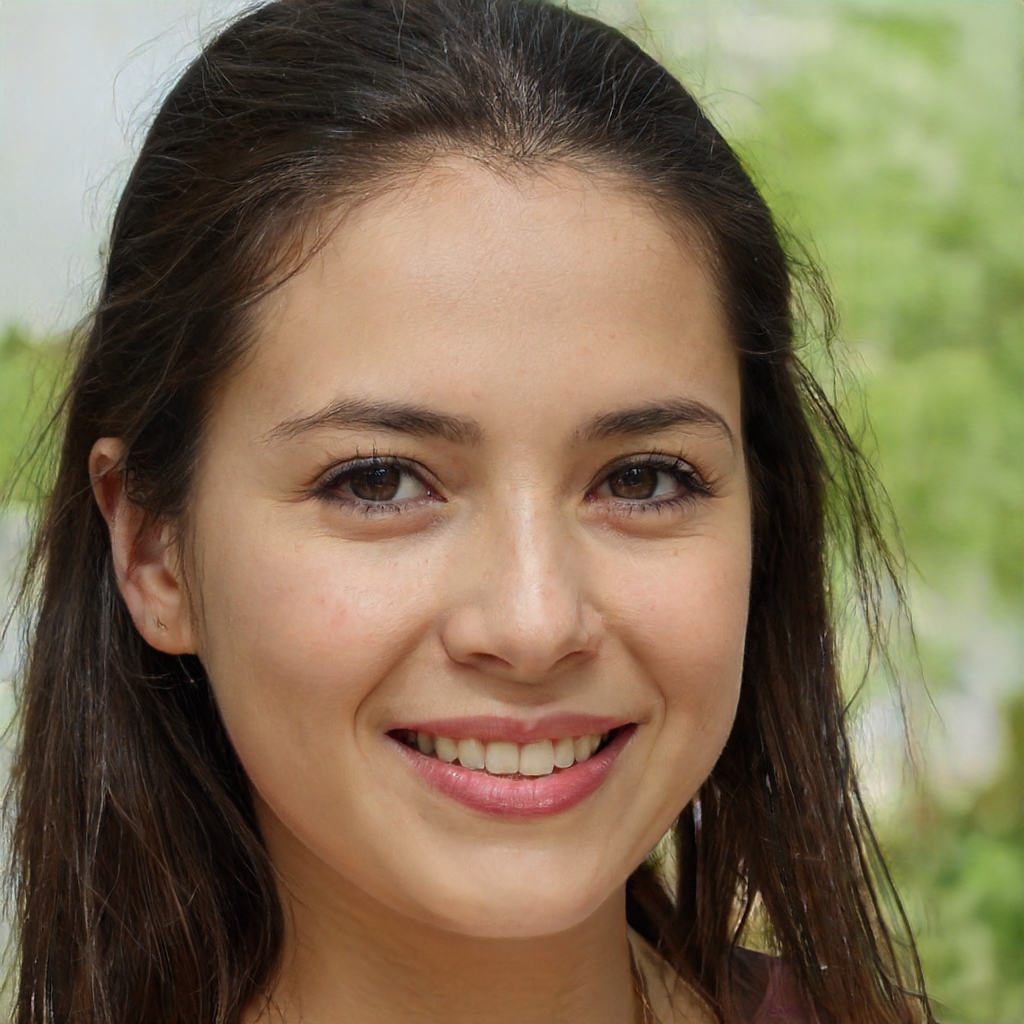
I am Administrative Assistant with eight years of experience working alongside the executive team.